IOT Enabled Condition Monitoring System
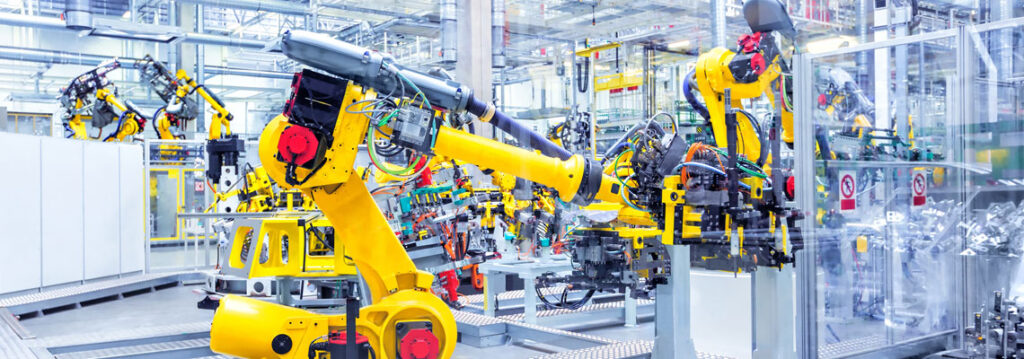
Predictive maintenance lets you monitor equipment health to avoid future failures during operation. It uses predictive algorithms with data from equipment sensors to estimate when your equipment will fail. It also pinpoints the root cause of problems in your complex machinery and helps you identify which parts need to be repaired or replaced. This way, you can minimize downtime and maximize equipment lifetime.
The process of monitoring the parameter of machinery (vibration, temperature etc.), in order to identify a significant change which is indicative of a developing fault. The use of condition monitoring allows for scheduled maintenance to take & prevent consequential damages and avoid its consequences .
The data collected can be used to establish trends, predict failure, and calculate remaining life of an asset. This new achievement in vibration monitoring technology is an ideal complement to traditional vibration analysis. The method is capable of detecting at a very early stage such machine problems which are generally difficult to identify early with conventional vibration monitoring techniques, such as gear and bearing damages.
Goal of CBM
The main goal of condition based maintenance is to help you optimize your maintenance resources by performing maintenance work only when needed. CBM makes use of the Predictive maintenance tools to detect, monitor, analyze and detect anomalies in machines.
Measurement Method
There are two types of vibration measurement methods “Permanent online vibration monitoring system” and “Portable off-line monitoring system”. Either one is selected generally depending on importance rank of equipment
Online Monitoring
Machinery that : is important
- Operates Constantly
- Cannot be Approached
- Deteriorates Slowly

Offline Monitoring
Machinery that : is important
- Is Minimal impact from Breakdown
- Is Easy to be Measured
- Deteriorates Quickly
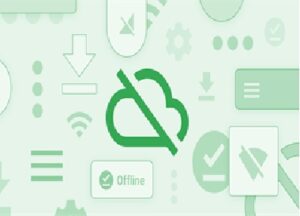
Our Solutions
Stand Alone Compact CBM System
- List Item #1
- List Item #2
- List Item #3
Gateway Based CBM Solutions
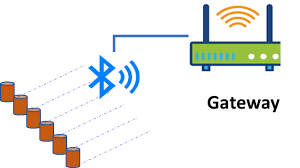
- 1. This solution will interact with gateway via Bluetooth Technology
- 2. Power supply : Battery operated
- 3. Gateway Interface : Ethernet
- 4. Can be interfaced up to sensor 256 nodes
- 5. API can be shared
- 6. Data on cloud and on premises solution
- 7. Stud Mounting easily
- 8. Firmware upgradation over the Air
- 9. Packaged solution with software hardware
- 10. Mobile app and dashboard functionality
- 11. Waterfall analysis ,Machine downtime etc
Controller Based CBM Solution
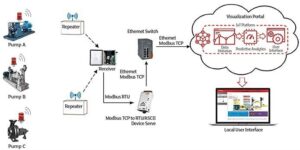
- 1. This solution consists of probe types sensors as per customized requirements
- 2. Cabled sensors can be extended as per requirement
- 3. This solutions is available for High temperature and vibration level requirements
- 4. This solutions addresses all reciprocating application needs
- 5. Needs dedication online/offline software
- 6. Hardware controller and accessories
How does predictive maintenance work?
Predictive maintenance uses historical and real-time data from various parts of your operation to anticipate problems before they happen. There are three main areas of your organization that factor into predictive maintenance:
- The real-time monitoring of asset condition and performance
- The analysis of work order data
- Benchmarking MRO (maintenance, repair and operations) inventory usage
There are several key elements to predictive maintenance with technology and software being one of these critical pieces. Namely, the Internet of Things (IoT), artificial intelligence, and integrated systems allow for different assets and systems to connect, work together and share, analyze, and action data.
These tools capture information using predictive maintenance sensors, industrial controls, and businesses systems . They then make sense of it and use it to identify any areas that need attention. Some examples of using predictive maintenance and predictive maintenance sensors include vibration analysis, oil analysis, thermal imaging, and equipment observation. Visit our condition-based maintenance page to learn more about these methods.

Cloud Based Predictive/Prescriptive Maintenance
- Our IIoT solutions enables Predictive and prescriptive maintenance strategies for key industrial assets.
- Mechanical, thermal and electrical parameters are gathered on a real-time basis through advanced sensors and using advanced analytics trends are Identified and alerts are issued prior to failure.
- Predictive condition monitoring is most appropriate for simple systems, where single variable math can be used to predict failure. More complex systems involve prescriptive condition monitoring, where multiple variables are analyzed to predict the failure.
- This requires more contextually driven understanding of operating conditions and more accurate diagnosis of the pending issue with fewer false positives.
Benefits of predictive maintenance
When predictive maintenance is working effectively as a maintenance strategy, maintenance is only performed on machines when it is required. That is, just before failure is likely to occur. This brings several cost savings:- Minimizing the time the equipment is being maintained
- Minimizing the production hours lost to maintenance
- Minimizing the cost of spare parts and supplies
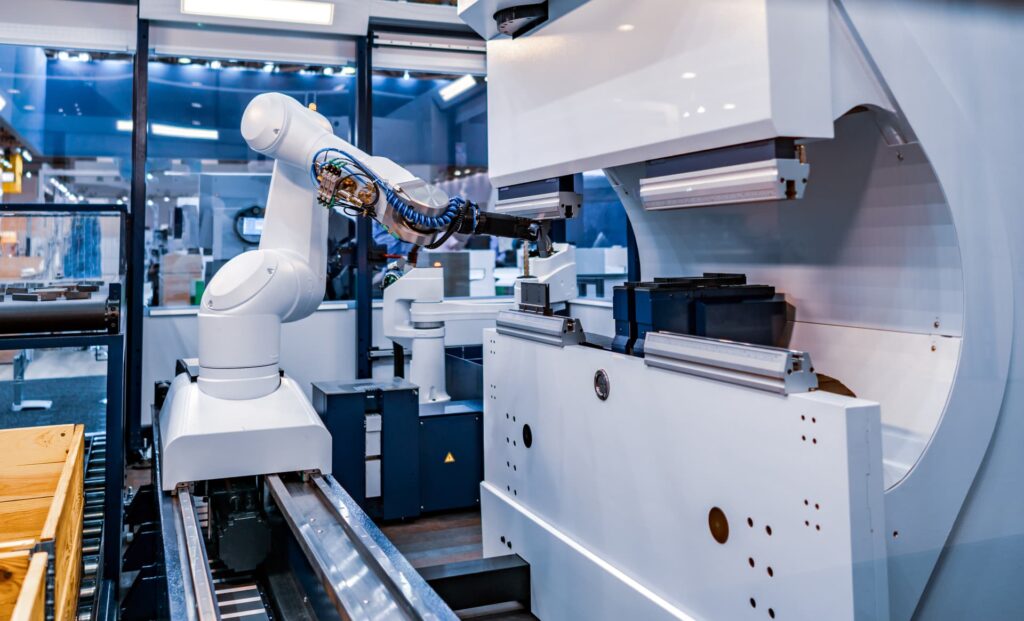
Applications
- Rotating Machines
- Underwater Submersible Pumps
- VNC
- Heat Exchangers
- Rolling Mill
- Pumps
- Gearbox
- Reciprocating Machines
- CNC
- Conveyor Systems
- Boilers
- Spindle Motor
- Motors
- ID & FD FANS
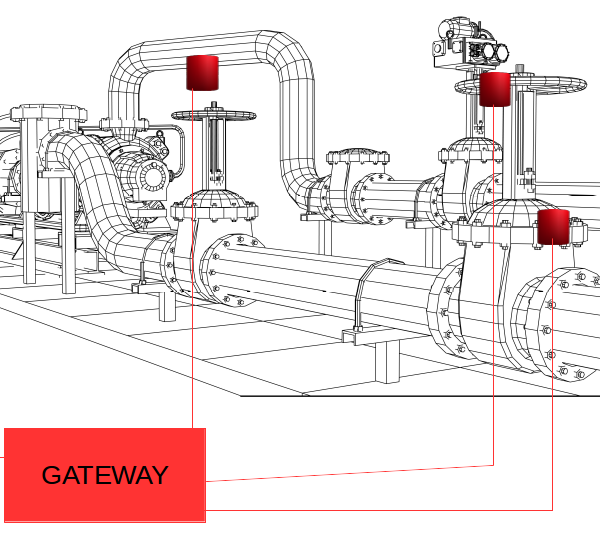
The Bottom Line
Predictive maintenance seeks to define the best time to do work on an asset so maintenance frequency is as low as possible and reliability is as high as possible without unnecessary costs.
Utilizing the Internet of Things is key for implementing a successful predictive maintenance program, as is the use of predictive maintenance sensors and techniques, such as vibration analysis, oil analysis, thermal imaging, and equipment observation
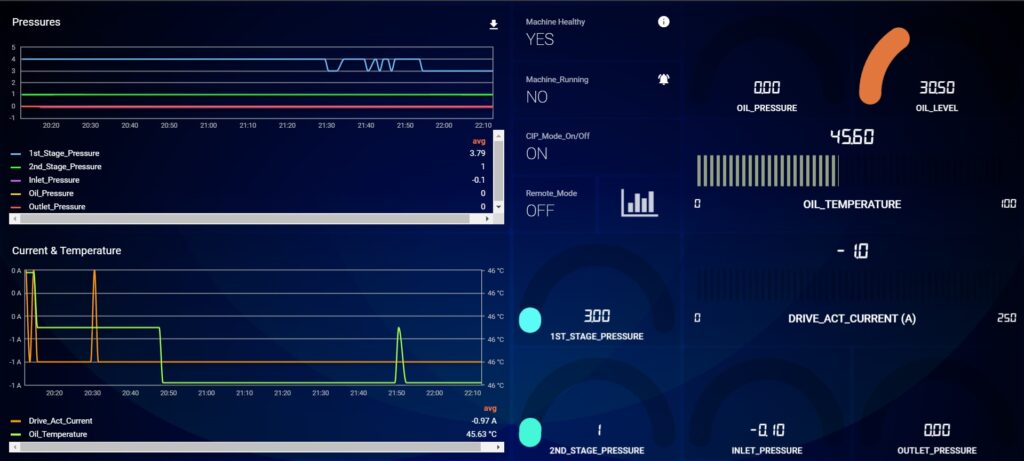