Cranes with IOT
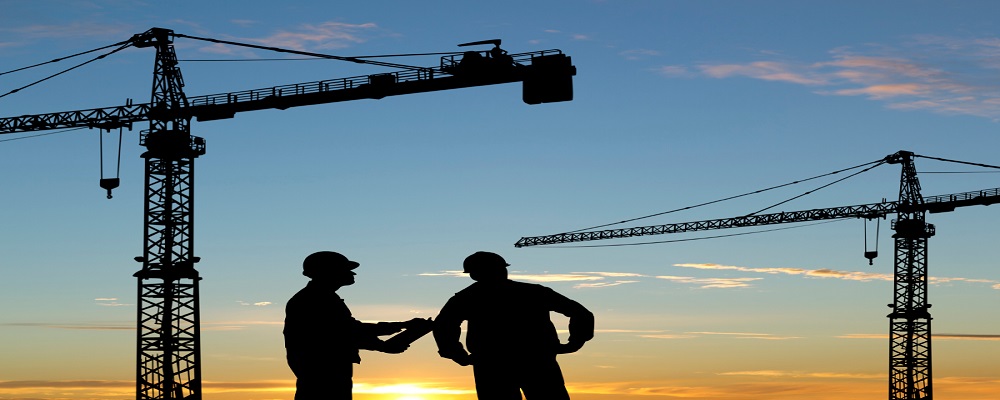
² Enhance safety and improve productivity via WSN-IoT
² Track progress and working reports
² Cloud base report analytics
² Optimize transportation and logistics planning
² Reduce operator fatigue
² Reduce labour costs and inventory tracking time
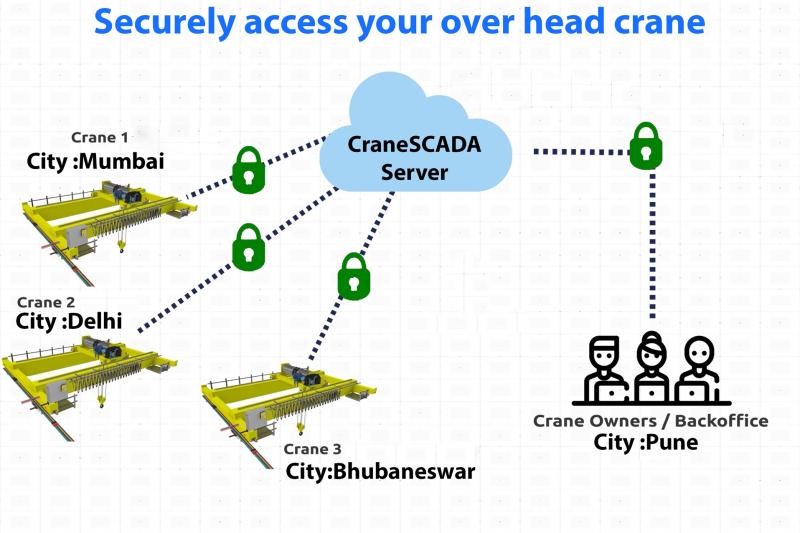
Remote Crane Monitoring Solution is a comprehensive IOT Crane solution which includes cloud data analytics and mobile application along with a hardware sensors which can be easily integrated or retrofit on indoor heavy material handling cranes such as EOT cranes, Double grider and single grider cranes, gantry cranes, bridge crane, JIB cranes, HOT cranes or outdoor mobile cranes such as tower crane, mobile cranes, telescopic cranes, container cranes etc.
Benefits for crane users
- Fully indigenous and integrated– hence reports, alerts, can be customized to your needs, crane configuration of various makes and models.
- Retrofit solutionwhich can be easily integrated on your existing cranes helps improve proactive and preventive service support of aging cranes.
- Provides crane usage, operating information, overloads,safety alerts that is used to assess crane condition and safety remotely at your fingertips with daily, weekly reports.
- Crane maintenance can be planned and optimized to reduce unplanned downtimeand to improve equipment safety, productivity, reduction in spares and improve crane life cycle value.
- Provides knowledge and notifies of the critical crane parameterssuch as operating info, remaining safe design working period (SWP), motor duty cycle, vibration, overloads, emergency stops, temperature and remaining service life of selected components such as hoist, vfd/plc, motor, brakes, ropes etc through emails alerts
Indoor Cranes remote monitoring and preventive maintenance parameters
- Motor voltage and current monitoring.This information is used to monitor the hoist, cross travel and long travel motor health. Advanced analytics (AI based algorithms) are used to detect anomalies and deterioration in the motor operation. This in turn gives an advanced notice to the user to carry out preventive maintenance thus avoiding costly breakdown.
- Motor temperature monitoring. This information is critical in preventing burnout of the motor which could be extremely costly. The system sends timely alerts when the temperature goes beyond a safe limit before it causes any harm.
- Hoist motor vibration. This is a long-term monitoring solution which tracks wear and tear of the motor over long period of time – months or years. The Artificial Intelligence based algorithm notifies the user when it is time for overall preventive maintenance of the mechanics of the motor. Higher vibration could be an early symptom of the imminent failure.
- Crane operation usage monitoring. Crane operational data is gathered from up, down, left right, north south button press and limit switch monitoring for hoisting, cross and long travel for crane movement . This is to keep track of how many times different type of movement was done on the crane. Later this information is consolidated to measure operational efficiency and remaining service life of Cranes.
- Motor CDF (Cyclic Duration Factor). Motor CDF is calculated using operational parameters and current and is used to alert the user in case CDF usage exceeds limits.
- Motor overload and load monitoring. Motor Overload and actual load is monitored using combination of current and load sensors. This information is used to track the crane usage within specified load conditions
- Motor brake faults monitoring. Brake Air gap is monitored using sensors. Brake fault alerts are sent if the air gap is beyond safety limits. This helps minimize the risk of load drop with the detection of brake faults
- SCADA, VFD, PLC monitoring.Monitoring system can interface to the automation systems with custom protocols for monitoring of control parameters, faults and status etc. This helps in further detailed analysis of crane operation conditions, faults etc.
- Safe Design Working Period(SWP) monitoring: Crane long term safe design working period is calculated using advanced algorithms using operational history, CDF and load conditions. This gives knowledge of remaining design working period and crane service life.
- Crane Rope Faults: Slack Rope faults are monitored and alerts are given instantaneously to avoid rope fault, load drop and other safety risks.
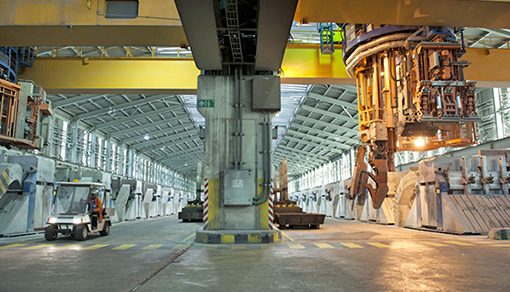
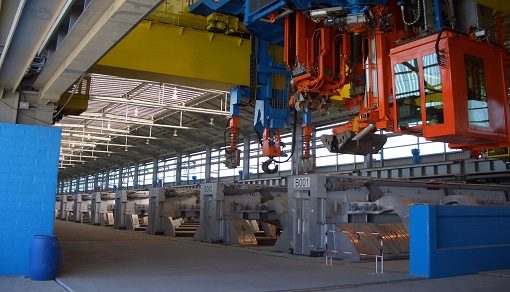
Outdoor Cranes remote monitoring and preventive maintenance parameters
The system collects following information using different sensors:
- Crane GPS Location tracking. GPS Sensors are used to track the location of your heavy material handling equipment such as mobile cranes.
- Vehicle Speed tracking: Sensors are used to track the vehicle speed of your heavy material handling equipment such as mobile cranes and alerts are sent if over speeding.
- Operational Information. Crane operating hours, meter reading information is a calculated using advance algorithms using combination of sensors to provide utilization information and predict maintenance activities.
- Safe Load indicator. Safe load indicator has the capability of detecting the angle, weight of load lifted, and ground radius of crane. Alerts are sent if the lift is exceeding the safe operating range of the machinery
- Crane Angle and Tilt Monitoring. Crane Angle and Tilt is monitored for safety conditions and alerts are sent if safety limits are crossed.
- Crane Accident & Vibration Monitoring. Crane accident and vibration is monitored using sensors and alert notifications are sent.
- Hydraulic Motor Pressure. This information is used to monitor the hoist, cross travel and long travel motor health. Advanced analytics (AI based algorithms) are used to detect anomalies and deterioration in the motor operation. This in turn gives an advanced notice to the user to carry out preventive maintenance thus avoiding costly breakdown.
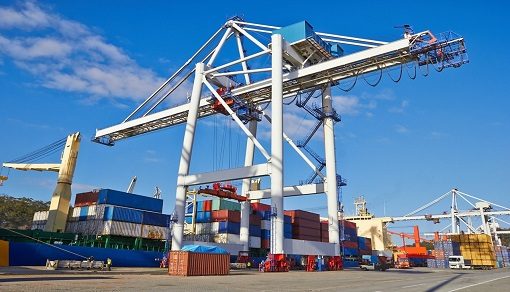
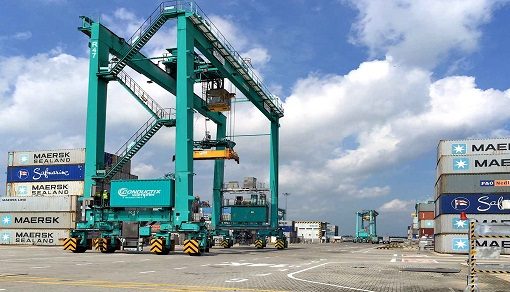
Crane Monitoring data analytics, reports and alerts
Crane Monitoring Cloud data analytics system has two prime functionalities:
- Dashboard and reports for Daily production / operations information.
- Alerts / alarms.
The standard daily and weekly reports are sent to the management using email. There is also a provision to demand the reports from the web interface.
Alerts are usually sent by email, sms or similar mechanism which would attract attention for quick corrective action.
The AI (Artificial Intelligence) based algorithms are used to baseline the reference behaviour of the electrical motor and brakes effectiveness. Any statistically significant variation from the base line is raised as an alert so as to avoid breakdown and allow of timely preventive maintenance and repairs.
Other features of the Crane Monitoring Preventive Maintenance system
- The system is equipped with remote firmware upgrade. Thus, to upgrade the firmware with new features or bug fixes, you do not need to make a site visit. Instead it can be done from your office itself.
- It has a small built-in battery which indicates tampering of the device such as removal of power, opening the box etc. This alert is sent to the server (within a few minutes) before the electronics loses power. This deters malicious tampering of the device.
- External devices such as VFD, PLC, data loggers can be connected to the system. The communication protocol of such devices needs to be known so that the same can be implemented in the system to work in coordination with existing electronic equipment.
- In case of loss of GSM signal, the system stores the data locally. This data is then uploaded to the server once the connectivity with server is restored. Thus, even in case of loss of connectivity, there is no loss of data.
- Lastly, since the hardware and software is designed and developed by ingenious Techzoid, we can make changes, add features, and customize any of the software screens, sensors, and features. This gives a unique advantage to the user to get custom made system developed on top of a proven indigenous platform.
